Digital Twins are transforming manufacturing - an interview with Servitly’s Stefano Butti by IBBAKA
Written By Steven Forth
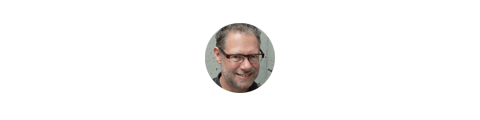
“All models are wrong, but some are useful.” George Box
Digital twins, when well designed, are among the most useful of models.
Over the past decade digital twins have emerged as a foundation for digital transformation in the manufacturing sector. A digital twin is the virtual model of a physical object. It could be something as small as a value or gear box, or as complex as the system that operates a large chemical plant. There is work ongoing to build digital twins of organisations and social systems, climate models can be thought of as a kind of digital twin, and there is work to build the digital twin of an individual by training a large language model with their writing and speech.
Virtually any piece of machinery that can be instrumented to generate data can be modelled as a digital twin. And manufacturers of all types are moving to make sure that they have developed digital twins of their key products and then connected them with data to create digital product-service offerings.
One company enabling this transformation is Servitly in the province of Como, Italy. Their vision for a digital twin architecture is shown below.
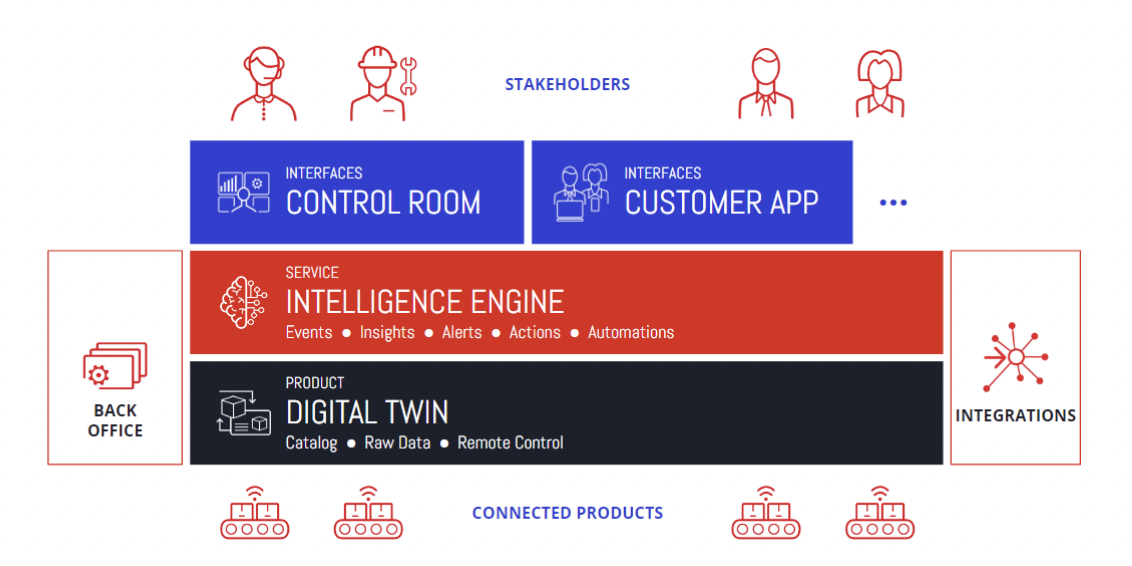
Ibbaka interviewed CEO Stefano Butti in October 2023 to get his insights into how the digital twins used by manufacturers are evolving.
Ibbaka: Digital twins are becoming a key part of the industrial infrastructure and they are critical to manufacturers of all types and sizes.
We would like to get your insights into digital twins and how the digital twin technology and market are changing and expanding. Before we dive in, can you share with us a bit about your background and how you came to start Servitly?
Stefano: I started as a software engineer and before founding Servitly, I was the co-founder and CEO of WebRatio, a software company building an application development environment. So I spent the first half of my career building an application development framework based on model-driven development. So this is where I began, with experience in the software domain, in application development, and being the CEO of a startup company.
Ibbaka: What then brought you to start Servitly?
Stefano: The ignition was because I was fascinated by two big transformations that were beginning in 2015. One was the Internet of Things (IoT). In 2015, we could consider that we were at the beginning of IoT. I was really fascinated by the concept of having physical objects connected to the internet and having access to an incredible amount of data produced by these things. This concept could, in my opinion, generate a very profound transformation.
On the other side, it was a very wide domain with many, maybe too many applications. I was also fascinated by another trend that is called ‘servitization’.
Servitization is not a new concept, but it started to gain traction because of IoT. Servitization transforms the business model of a manufacturing company or a product company by adding value-added services on top of the product, and in some cases transforming products into services.
I was really fascinated by the concept because I think this is the only way to face the problem of sustainable growth in terms of consumption, population and resources. As a society we need to move from a purchase and disposal approach to a service approach, where products are being used for a purpose, but then reused, recycled, etc.
The conjunction IoT (Internet of Things) plus servitization is equal to something new. Something new that could have a very profound impact on the economy, society in general, and the world. So I was really keen to play in this game, and since I am a software engineer, and the people I worked with were all software engineers, we faced this problem from a software point of view.
Servitization is a big, profound transformation. Let's address one of the problems: software. We started Servitly with the idea of providing software specifically designed to help manufacturing companies take the opportunity to exploit IoT, to change their business model.
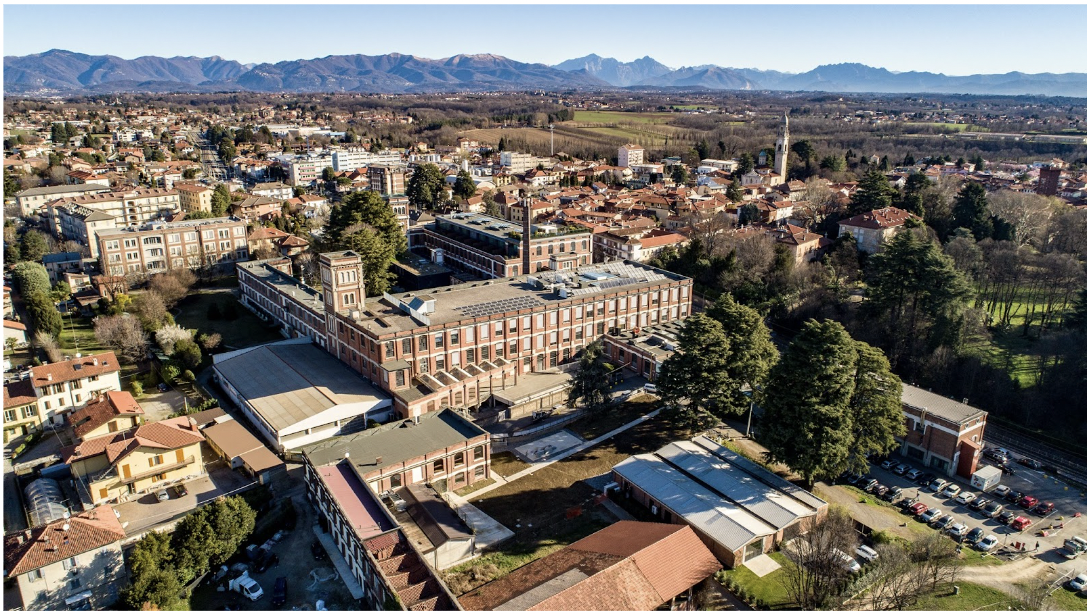
Ibbaka: Servitly is located in the Como area of Italy and I believe it is one of the world's centres for advanced manufacturing. Did your location have any impact on your choice of direction for the company?
Stefano: Yes, because here we have the opportunity to talk with a very large number of key manufacturers. In the northern area of Italy, there is a very high concentration of key manufacturers working for the food industry, for example, but also the packaging and hvac industry.
This is one of the biggest regions in the world with key manufacturers and it wasn’t by chance that we started working with them. In and around Como we can have a lot of connections and a lot of conversations.
We understand IoT and servitization. It would be great if we could exploit this to start something new. So yes, the location of our company is a crucial aspect of our existence.
Ibbaka: Can you tell us what a digital twin is?
Stefano: So there is a lot of confusion about this term. It is like other words like ‘Internet of Things’ or even ‘servitization’. I anticipate that many people will not have the exact same definition. So a very broad definition is the digital twin is a digital model of a physical object.
This physical object could be anything: a city, a house, or a plant. At Servitly, we are only thinking about digital twins of physical objects, like an oven, a boiler, or a machine tool. The digital twin is a digital model. It means that in the digital world, work managed by software, we create a copy, or sort of copy, of the product or the machine in order to use this model in two large phases.
One type of digital twin is useful when designing a product. So in this case, the digital twin helps the design team make simulations and do 3D modelling. Maybe some testing is done in a digital space before even building the product.
Then we have an operating digital twin. Once the product has been built and installed in production and it is operating, we can have a digital representation of what the machine is doing. So thanks to IoT, connectivity, to sensor data, we can collect data from a boiler, for example, or a machine tool, and consume this data in order to say, ‘What is the current operating condition of the boiler?’ ‘What is the current temperature?’ ‘What is the current level of pressure?’
So in this case, the digital twin is used to support the operation of the machine. We are focusing on this at Servitly. This second type of digital twin, the operating digital twin.
Ibbaka: What sort of benefit are your customers getting from having these operating digital twins?
Stefano: One major benefit is enhancing support and maintenance operations, fulfilling support and maintenance service contracts, or even, if there is no service contract, fulfilling warranty obligations. All manufacturers have some support activities. Having a digital twin of the product is an incredible help in cutting the time in understanding what is the problem. An operating digital twin can really save a lot of time in normal service operations. This could be a great help. And this is only the beginning. Once you have a digital twin, you start thinking about preventing failure. I have more information when something happens so I can act quickly, but then you realise that you can even prevent failure.
This anticipates the second reason why our customers are using digital twin operating digital twins. To enhance their value proposition. They can offer their customers something valuable. For example, increased uptime for the machine: reduce the downtime; reduce the failure rate; or even increase production or increase the quality.
The digital twin is the foundation of something new, a new value proposition, and new revenue streams.
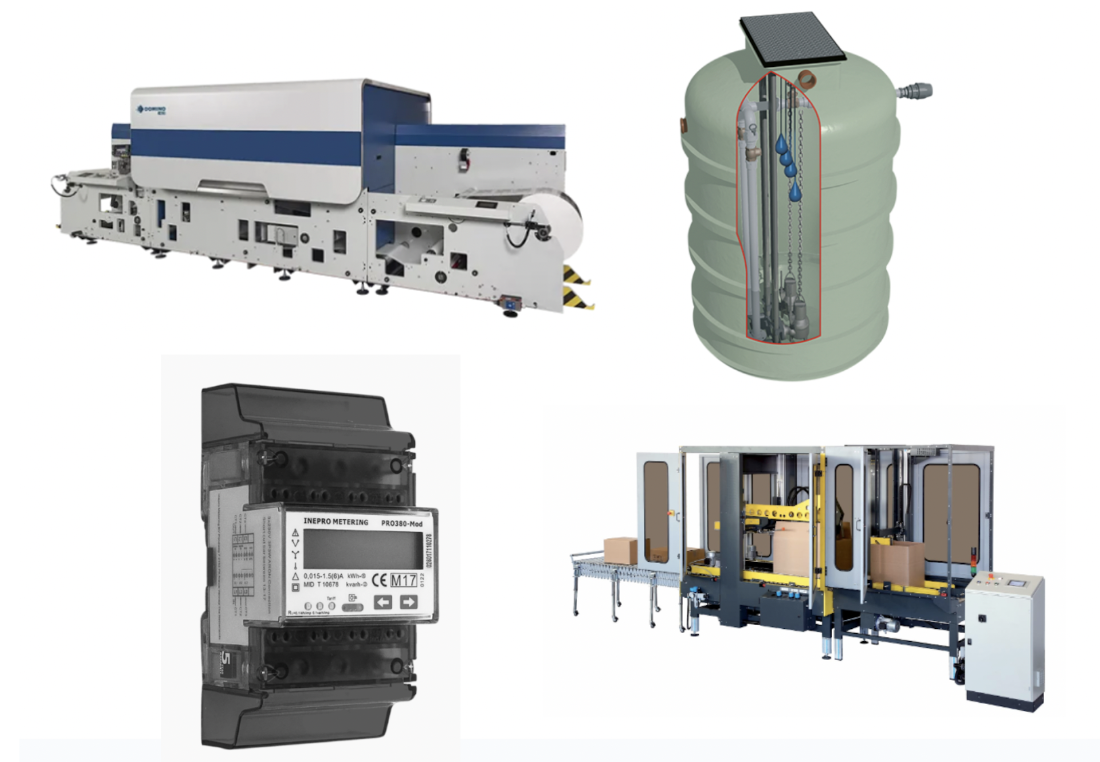
Ibbaka: Do you think that digital twins, as they become more and more adopted, are going to change how the products themselves are designed?
Stefano: Yes. In the beginning, you had a digital twin on top of an existing product. But we saw that once our customers started receiving data, they started to understand the value that is inside this data. They understand that the digital twin could be enriched. There is a simple way of creating a digital twin that is inside any machine. There is an electronic controller that is the brain of the machine, so an electronic controller that controls the machine. The easiest way to create a digital twin is to connect this controller to software and start collecting the data that runs inside this controller. This is relatively easy, but then you realise that you want even more data.
For example, let's talk about food equipment. We talk with many food equipment manufacturers. For any food equipment, the final result is what counts. So the quality of the coffee, but also the quality of pizza, the quality of bread, the quality of pasta.
Quality is one of the values that an oven and an oven operator take care of when using this oven, but quality is the worst sensor in value because there aren’t quality sensors currently in ovens. This is an example of what happens when a manufacturer starts moving from selling technical features of ovens to selling the quality of what is baked.
If you sell quality, you immediately have the need to measure quality. This comes back to the digital twin. The digital twin needs to know something about quality. This means that the oven should have some sensors that could detect the conditions that determine quality.
So this is an example where thinking about value generated for the customer and having a digital twin. Let the manufacturer come back to the research and development department and say, “Okay, we need to change how we design the oven because we have to add some sensors or maybe we have to make some adjustments because we really want to measure quality.”
Since we measure quality through a digital twin and rely on data, we can design the product to feed the digital twin in order to maximize the value extracted from this data.
Ibbaka: Do you see that digital twins, and servitization more generally, will lead to new business models for manufacturers so that they have new ways of taking their capabilities to market and earning money?
Stefano: Yes, I see this, but I will also say that given how the manufacturing industry is, change will come slowly. Other industries, retail for example, or fashion, have very, very fast changes. The manufacturing industry has slow changes. I'm confident and this is the direction we are going, and what we will see in the coming years.
Every manufacturing company we work with is upgrading its business model. They are adding new sources of revenues, but also new competition. New revenue comes from a new value proposition and that is a competitive weapon. The reason for this is that if you compete only on product, or technical features, many European equipment manufacturers will lose against Chinese or Asian competition.
Chinese and Asian competition were once low cost and low quality, but now they are moving to low cost and high quality. So working only on product features is not enough to compete. This change is behind the search for new ways of generating revenues and new ways to compete.
Digital twins are not only about measuring and presenting data. The digital twin opens the possibility for a manufacturer to also develop its intellectual property. It gives a competitive advantage in how it manages data in order to protect its intellectual property.
This is important because this is what we see in our customers. We design exactly for this purpose. We understand the manufacturer can do a lot with data because a manufacturing company knows every single piece of metal and single electronic device inside the mesh and machine.
They have a lot of knowledge on how to extract value from this data. Extracting value could mean predicting a failure, or suggesting to the customer how to operate the machine in order to save energy or increase quality. This knowledge is there, inside the manufacturer, so they can work not only on the technical specifications but also on how they can transform data into value.
This could be a compelling competitive advantage that helps to change the business model. The natural evolution of this is that instead of selling a product, you sell the outcome. The customer buys a product to get results.
Ibbaka: Digital services platforms collect a great deal of data. North Americans are very interested in the data privacy laws in the European Union. Is the data that you are collecting or that these platforms are collecting covered by any laws? Does the Internet of Things introduce new security risks? If so, how can these be managed?
Stefano: Yes, there are data regulations, and we have to distinguish personal data from machine data. Regarding personal data we have in Europe the well known "GDPR".. Something similar is happening also for machine data. It is the "Data Act", a new EU regulation that will enter into force in 2025.
Data Act is very interesting because it will give a solid legal foundation to let equipment manufacturers and service providers manage data ownership and exploitation.
When our customers sell the machines with the digital twin, they also have a contract that says, “Okay, you accept that as a manufacturing company, we collect the data from your machine and you accept this and this is regulated by this contract.”
Data Act will normalize and standardize this approach. For example, you have a machine tool and I, as a manufacturer, offer you a digital twin solution, a digital service solution, or even an equipment-as-a-service solution.
But I need data in order to operate. So if you want this, you’ll have to accept that I get some data from you. Otherwise, I cannot provide this service. In this way, regulation will not be a problem because I always say that if there is value it is in both parties interest to exchange that data.
If a customer is hesitant, perhaps it’s due to the fact that they don't perceive or acknowledge the value. If there is value and economic gain, or even non-economic, you will exchange data for value.
Ibbaka: For companies thinking about the evolution of digital twins over the next 3 to 5 years, what directions do you see coming?
Stefano: I think that digital twins will develop in two directions. One is richness in terms of how many different types of data there are used. Today we are starting with digital twins that are only the replica of the electronic controller inside the machine. But now manufacturers are adding more sensors. Digital twins now cover maybe only health, or an alert, or failure. In the future, they will evolve in order to cover any relevant aspect of a machine.
The other direction I see is more granularity. Today, the granularity of data is limited by connectivity.
Maybe the machine is connected to a cellular operator, so there are some limitations in how much data I can collect due to bandwidth or even cloud costs. A digital solution incurs costs in managing data and storing data, but as we know, technology is progressing fast.
In a few years, the cost of cloud computing, and the cost of connectivity bandwidth is falling by half every year. In the future we will have digital twins that are closer to real-time than today. Maybe today we have information once a minute, then in the future, it will be once a second or even less.
With a network that will allow faster communication and provide for larger bandwidth data exchange will approach real time. The digital twin will also approach real-time updating. This would lead to closer two-way communication. The digital twin will not only be reading data, but also interacting with the physical object. So the digital twin talks to the physical twin and says, okay, now you need to change something.
In the future, I think digital twins will evolve also in managing two-way communication thanks to connectivity and more reliable connectivity.
Ibbaka: This may be a bit of a stretch, but do you think that there are going to be opportunities to shift functionality from the physical space to the digital space? In other words, is there functionality that currently occurs in the physical space that could in the future occur in the digital space?
Stefano: I'm uncertain about that in the future. The key question is how much computation will reside on a central system versus the 'edge.'
For instance, certain functions in a car make sense to remain local for security and safety. However, other functions could run in a central cloud, existing solely in the digital realm.
Both cloud and edge computing capabilities are on the rise. Cloud data centers are becoming more powerful, and embedded computers in products like smartphones, cars, and even ovens are also gaining strength. It is unclear where functions will ultimately reside. What is certain is that software will continue to play a pivotal role.
Software's influence extends not only to the cloud but also to the edge. The question should not solely revolve around location (cloud or edge) but whether software can replace physical functions. Indeed, the adage that 'software is eating the world' holds true, and software is increasingly taking over tasks previously handled by mechanical or electrical devices.
Ibbaka: Some have said that “If software is eating the world, then AI is eating software.” What role do you see advances in artificial intelligence playing for digital twins?
Stefano: I see both risks and opportunities.
The risk lies in the potential of artificial intelligence in replacing the manufacturer's knowledge of how their machines work. For example, consider a boiler manufacturer. Intelligent heating controls using AI can determine the right time to activate or deactivate heating systems, potentially replacing the manufacturer's control systems. This poses a threat to their authority.
However, there is also opportunity. Artificial intelligence allows manufacturers to build models, giving them more control and the ability to predict machine failures. This could prove highly beneficial if they can govern the AI's operation to suit their needs.
Before fully embracing AI, there's value in transferring human intelligence into a digital system, which can also be termed artificial intelligence. This traditional form of AI involves systems that make decisions based on established knowledge.
We are currently assisting manufacturers in instructing digital twins to provide suggestions based on detected conditions. This simple yet effective form of AI offers substantial value. Additionally, machine learning presents the next frontier, where machines can discover unknown information for manufacturers, enriching their understanding of their machines.
Ibbaka: So if you were advising a manufacturing company today that was considering adopting digital twins and moving to more of a service model, what are the key pieces of advice that you would give them?
Stefano: The most crucial step is to just get started. Even if it's with a basic solution, the key is to start as soon as possible. The reason for this urgency is based on what I've observed in our customer base. I refer to it as the 'epiphany of data.' Manufacturing companies that haven't yet developed a digital twin for their products are essentially operating in the dark. They are unaware of their own potential.
My recommendation is to begin as early as possible, even if it means starting with a rudimentary and somewhat patchwork solution. Commence the data collection process and create a minimal viable digital twin without delay. This initial step will help awaken your awareness of the data's value.
I've noticed that when our customers embark on this journey and start examining their data, they often experience a revelation. They begin to realize the wealth of information they can obtain, such as machine operating hours and usage patterns, which they were previously unaware of. This newfound insight sparks their imagination about the possibilities of what they can achieve with data.
The key takeaway is to start collecting data promptly, even if it begins with just a small set of metrics. The specific data details aren't as critical as the shift in mindset. It's the first step toward establishing a data-driven approach within the company.
Ibbaka: So your critical advice is to get started collecting data and to begin the analysis and model development process so that you can be on the road to continuous development and improvement?
Stefano: Precisely. It's essential to involve as many departments as possible in this process. Sometimes, we come across digital twin initiatives that are exclusively managed by the research and development team. It might be seen as something they're handling independently, driven by customer requests or their own preferences, while other departments, such as the service or marketing teams, or even the CEO and the board, remain unaware of these efforts.
However, data should be instantly shared across the entire company because all departments in a manufacturing company can benefit significantly from harnessing data. This inclusivity is key to maximizing the potential of data.
I'm really excited to play this role in this big game.